What is upskilling and how does it apply to the automotive industry?
A recent edition of the Financial Post ran a story about how Canada’s auto industry is training for a wave of jobs never seen before. The story opened:
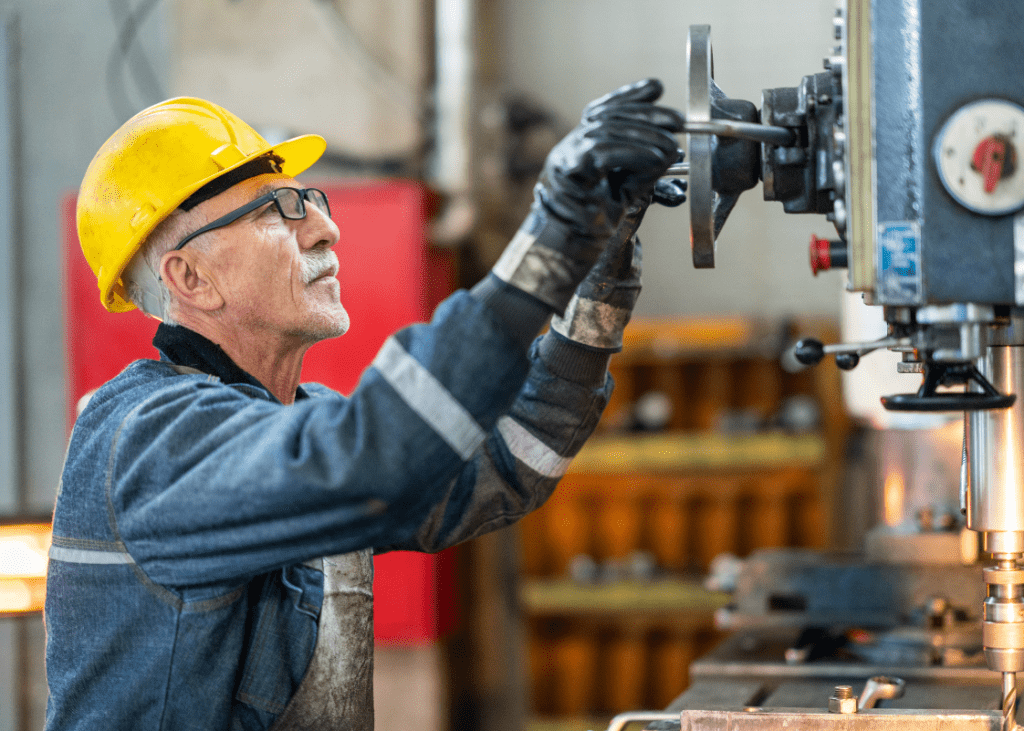
“Car models being imagined now look nothing like the ones in our driveways today – and that means Canada’s automakers and suppliers find themselves posting more jobs requiring skills that aren’t yet widely taught on the job. Many companies are taking the matter into their own hands, teaming up with colleges, universities or online platforms to recruit and retrain a bespoke workforce for one of the biggest industry shifts in a century.”
Upskilling defined
Expressing this industry shift in a single word is simple: upskilling. Simply put, upskilling is when an employee acquires advanced skills through a process of education and training.
And that is what the FOCAL Initiative stands for. Our task is to see where the automotive industry is trending and be fully prepared for the tectonic shift for that transition process—which is already occurring—and how it impacts both employers and employees.
The importance of upskilling in principle
A company’s ability to upskill, or its capacity for training and developing its employees to expand their skillsets, creates a significant competitive advantage. It’s a two-way street delivering tangible benefits to both employer and employee, with proven implications for productivity and efficiency, morale, job satisfaction, employee retention, loyalty and more.
In today’s economy, where skilled labour shortages and job postings remain unfilled, upskilling is a core strategy that impacts the long-term competitiveness of any company to which the process is applied, driving operational efficiency and delivering tangible benefits to the bottom line.
The importance of upskilling for the shift from ICEs to EVs
Perhaps nowhere in the automotive sector is upskilling more crucial than in the shift from the internal combustion engine (ICE) to electrically powered vehicles (EVs).
In large part, it’s a digitally driven transformation. The conventional vehicle powertrain consisting of an engine, transmission, and drivetrain components will shift to batteries, motors, and a host of other electronic components.
With the adoption of EVs, the research and development (R&D) landscape will grow substantially. The EV ecosystem is more data intensive and digital compared with the traditional ICE vehicle ecosystem, resulting in new data services and business models being created, which will in turn create new—though different—jobs.
EVs have fewer mechanical parts than the traditional ICE vehicle. Repairing EVs requires sophisticated electronics diagnostics, working with high voltages and servicing of batteries and other digital components.
The pivot from many mechanical parts (fuel pumps, starters, pistons, etc) to charging stations, battery chemistry and management, regenerative braking and more will impact workforce requirements. And that’s just the beginning.
The transition to electric vehicles will substitute many current jobs with new jobs
The headline in a recent report from Electric Autonomy Canada sums up the implications of the transition perfectly: “For OEMs (original equipment manufacturers) and parts makers, EV retooling isn’t just about plants — it means replacing lost jobs and upskilling their workforce.”
The reality is that, as Electric Autonomy Canada reports, “the transition to electric vehicles will cost jobs as well as create them, while requiring Canada’s auto labour force to acquire new skills – realities that governments and the private sector are now grappling with.”
Electric Autonomy Canada also offered an example of how, through their Automotive Manufacturing College (AMEC), GM are preparing their current employees for the EV transition: “Participants are taught how to carry out electrical procedures including: schematics, diagnostics and vehicle wiring harness construction. The program provides a full paid salary during the training period (which lasts between six to 12 months) at GM’s Global Technical Center.”
The human implication of upskilling comes from a, perhaps, unlikely source: Wayne Gretzky. He once observed that a good hockey player plays where the puck is. A great hockey player plays where the puck is going to be. And that’s the mindset behind the upskilling component of the FOCAL Initiative as it unfolds in 2023 and beyond.
How FOCAL supports upskilling
The FOCAL Initiative is a collaboration between the Canadian Skills Training and Employment Coalition (CSTEC), the Automotive Policy Research Centre (APRC) and Prism Economics and Analysis. FOCAL stakeholders (past and current) include Ford, Toyota, General Motors, the APMA, Magna, Woodbridge Group, Martinrea, UNIFOR, United Steelworkers and the Trillium Network for Advanced Manufacturing as well as representatives from all levels of government. FOCAL is funded by the Government of Canada. To learn more about our current objectives, please read Phase II goals: what’s next for FOCAL.
Follow us to stay informed
We’ve got a lot of work ahead of us and we’re geared up to handle it. Please follow FOCAL on LinkedIn, Facebook, Twitter and Instagram to stay informed about the progress we’re making and gain access to resources and special events as well as funding opportunities for employers.
We encourage everyone reading this blog to share it with their professional networks to best share these opportunities with automotive sector staff and employers. Again, the FOCAL team welcomes your questions and feedback – you may contact us at your convenience.