Why now is the optimal time to upskill your best workers
As the automotive sector continues to move forward—albeit against the headwinds of a sluggish economy—even the most progressive automakers, parts manufacturers and vehicle assembly businesses may be faced with decisions about layoffs.
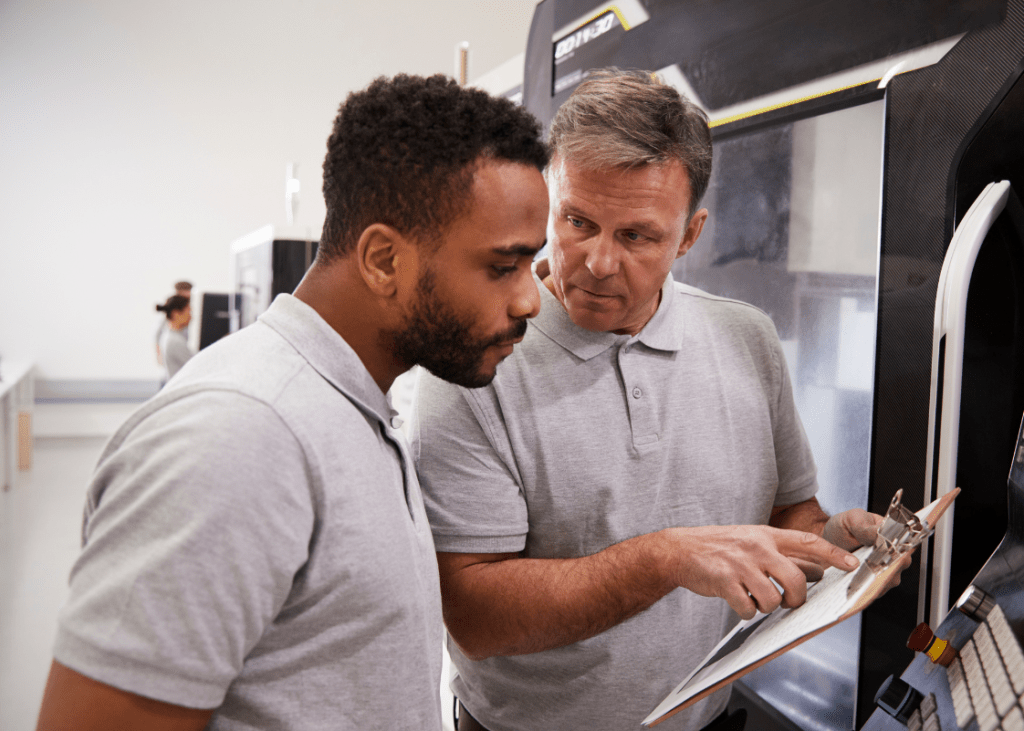
Numerous factors including inflation, interest rates, supply chain issues and the lingering economic impact of nearly three years of the COVID-19 pandemic, have taken an inevitable toll. Anticipating, understanding and offering practical assistance to businesses dealing with these challenges are a key part of the FOCAL initiative’s objective.
Consider this scenario
- You have a recent graduate employed at your company. Digitally literate and well-trained, they are hardworking, motivated and imaginative.
- But, due to economic conditions largely beyond your control, you are faced with an unpleasant reality that the individual in question—and perhaps a few others with similar skills and aptitudes—must be let go.
- You want to keep the talented individual, not to mention others bringing similar value to your company, but the bottom line must be considered.
- Layoffs due to losses has historically been the obvious verdict. It’s a solution long considered and reluctantly taken, but it’s the most logical option. Or is it?
Layoffs are often a default response to a temporary challenge. The cost of savings associated with layoffs tends to be overshadowed by bad publicity, loss of knowledge, weakened employee engagement, higher voluntary turnover, and lower innovation—all of which hurt productivity and profits in the long run.
How to avoid a self-destructive short-term decision
Consider the findings of a 2018 Harvard Business Review analysis entitled Layoffs That Don’t Break Your Company before taking what might turn out to be a self-destructive short-term decision.
States the Harvard Business Review: “The research clearly shows that bad layoffs and layoffs for the wrong reasons rarely help senior leaders accomplish their goals.” Drawing on corporate examples ranging from Nokia, Michelin and AT&T, and supplemented by a wide range of rigorously researched academic studies undertaken in North America and Europe, the Harvard Business Review investigation observed:
“A few companies have been experimenting with better ways to handle their changing workforce needs. Take AT&T. In 2013 the company’s leaders concluded that 100,000 of its 240,000 employees were working in jobs that would no longer be relevant in a decade. Instead of letting these employees go and hiring new talent, AT&T decided to retrain all 100,000 workers by 2020.
That way, the company wouldn’t lose the knowledge the employees had developed and wouldn’t undermine the trust in senior management that was necessary to engagement, innovation, and performance. So far, the results seem very positive.
In a 2016 HBR article, AT&T’s chief strategy officer, John Donovan (now CEO of AT&T Communications), noted that 18 months after the program’s inception, the company had decreased its product development cycle time by 40% and accelerated its time to revenue by 32%. Since 2013, its revenue has increased by 27%, and in 2017 AT&T even made Fortune’s 100 Best Companies to Work For list for the first time.”
Why retain, retrain and upskill talent under adverse economic conditions?
Not all companies have the financial resources of AT&T necessary to retain, retrain and upskill talent under adverse economic conditions. We know that far too many companies tend to prioritize short-term financial results over the long-term well-being of their employees. It’s a fact of life, whether the company occupies the automotive space or not.
However, evidence suggests that layoffs often act as an excuse to avoid difficult performance decisions, resorting to self-destructive ‘rank and yank’ tactics which—without the use of meaningful performance reviews and employee development plans to cultivate a base of high performers—do more harm than good.
The practical question is: why is an economic slowdown/downturn a good time to upskill your employees? The answers are simple and unequivocal.
1. To save money in the long run
The savings from upskilling vs. rehiring – an inevitable consequence of layoffs in a downturn – are generally substantial. Hiring new talent during an economic upswing instead of upskilling your current team in anticipation of one, requires a disproportionate investment of finances, time, and energy. Developing skills from the inside mitigates the risk you take with outside hires who may turn out to be a poor fit. This is true across many lines of business—even the owner of your local corner store will tell you it’s more profitable to upsell an existing customer than find a new one. The same principle applies to talent in the automotive industry.
2. Because upskilling is a necessity
Continuous learning, which is what retraining and upskilling imply, is not an option in the automotive industry. It’s an imperative. It’s hard to argue against the benefits of a more connected, invested, and engaged team – the consequence of disciplined hiring, stringent performance metrics, and a corporate culture that builds skills to weather change. Yo-yoing between over exuberant hiring during growth and damaging staff reductions when demand falls is a recipe for disaster. Don’t waste talent; nurture it.
That means understanding Industry 4.0
The Canadian automotive industry has been significantly impacted by the digitization of manufacturing, widely referred to as Industry 4.0. The FOCAL Initiative has concluded that Industry 4.0 technologies will have significant but manageable impacts on Canada’s automotive sector, especially as that shift affects current employment levels and future training, upskilling and hiring practices.
- 80% of jobs performed by production occupations will be affected through the partial or full elimination of certain tasks.
- 50% of skilled trades tasks will be equally affected.
- The industry will also be affected by the creation of new job titles reflecting the increased requirements for digital skills.
Putting it all into perspective
In an earlier post, we referenced The Future Skills Centre, a Toronto-based pan-Canadian initiative with close connections with The Conference Board of Canada. They recently published a briefing called Rising Skills: Digital Skills Needs for Smart and Connected Vehicles.
The briefing is upbeat. It recognizes that – sluggish economic conditions or not – even though the automotive industry shift toward smart and connected vehicles is affecting automotive manufacturers and, for example, parts makers, the case for retraining and upskilling has rarely been more compelling. Specifically, the briefing states:
“Automotive tradespeople are grappling with future work challenges related to connected, autonomous, shared, and electric (CASE) vehicles. Automotive service technicians, auto body and collision technicians, heavy-duty equipment technicians, truck and transport mechanics, and other tradespeople need technical, problem-solving, communication, and other 21st-century digital skills to thrive in response to these trends.”
And that’s where the FOCAL Initiative comes in. In case you missed it: the specific objectives of the FOCAL Initiative can be found here.
Follow FOCAL to stay informed
We have a lot of work ahead of us and we’re geared up to handle it. Please follow FOCAL on LinkedIn, Facebook, Twitter and Instagram to stay informed about the progress we’re making and gain access to resources and special events as well as funding opportunities for employers.
We encourage everyone reading this blog to share it with their professional networks to best share these opportunities with automotive sector staff and employers. Again, the FOCAL team welcomes your questions and feedback – you may contact us at your convenience.